By now, most of those involved in shipping bulk cargoes know that some commodities can undergo liquefaction. Quite what that means is less well known, but it is very well publicised that it can result in ships sinking. Articles regularly appear setting out how many ships have been lost and the number of people who have lost their lives when their vessels have got into difficulties during carriage.
There is much less information available on the “nearly” events, or even the “we worked hard to avoid” events. I have personally been involved in a substantial number of both of these. Timely advice and/or intervention can save ships and lives. I’m pleased to be able to say that no vessel I have been involved with has subsequently been lost. Suffice it to say that the cost to the industry of problems arising from liquefaction generally is very high.
IMO categorises bulk cargoes which can liquefy as being in cargo Group A.
To comply with the regulations, the moisture content of a Group A cargo needs to be below the transportable moisture limit (TML).
Concentrates or other cargoes which may liquefy shall only be accepted for loading when the actual moisture content of the cargo is less than its TML
IMSBC Code 2020 Edition paragraph 7.3.1.1
What is TML and how is it measured? In a classic example of circular definition, the Code tells you that TML is
Transportable moisture limit (TML) of a cargo which may liquefy means the maximum moisture content of the cargo which is considered safe for carriage in ships …
IMSBC Code 2020 Edition section 1.7
A later post will discuss the tests, as these and how they work is a whole topic in itself.
Liquefaction is a bulk property. One common misconception is that liquefaction involves cargoes becoming a liquid, and indeed the IMSBC Code uses this word to describe a flow state. Many liquefied cargoes however do not behave like liquids. “Fluid behaviour” is perhaps a better term to use.
As a physicist, I will introduce the concept of a phase change, as I believe the analogy is helpful. To a physicist, a change of phase involves a material changing from a state in which it has certain properties to a state where it behaves differently. An obvious example is melting a solid such as ice. Whilst the ice is frozen, its behaviour is like other solids. Melted, it becomes water which can be poured, sloshed, and so on but it is chemically still H2O. The phase change we refer to as melting involves the input of energy. So does liquefaction. A solid bulk Group A cargo can may enter a fluid state if conditions are within certain limits and with the input of energy.
A very widely viewed video shows a wheelbarrow full of soil undergoing liquefaction when energy in the form of vibration over a set of cobblestones is input.
Back in 2009, the year ASIAN FOREST and BLACK ROSE sank in India, I created this diagram.
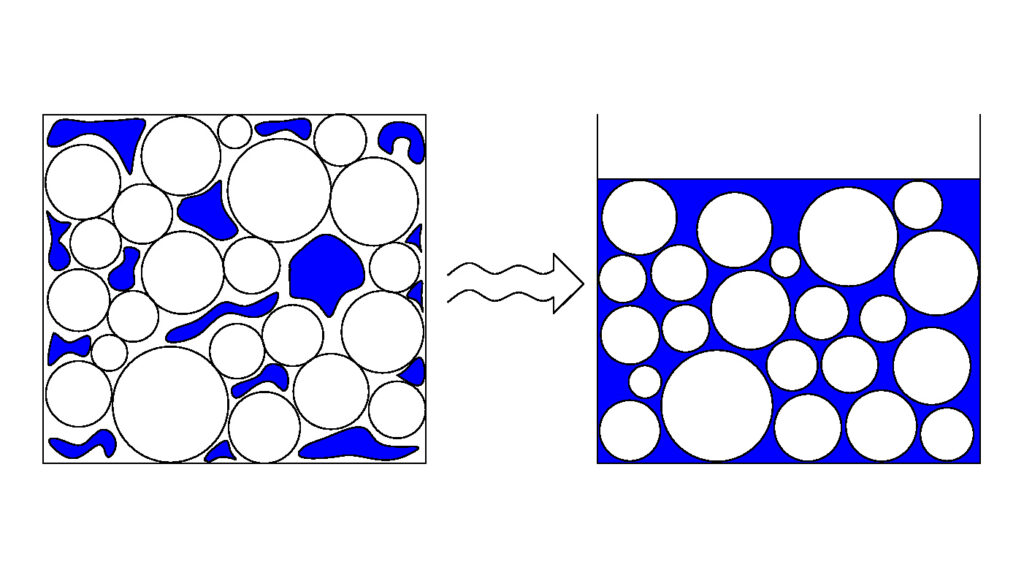
Facsimiles of this illustration exist, even variants where the particles are not circles/spheres. All the attempts to “improve” on my illustration/concept focus on aspects of it which didn’t really need to be updated/modified.
In this example, the assembly of particles is shown to be a collection of spheres (circles in cross-section). That wasn’t chosen because it matches the particles in a cargo of iron ore or nickel ore, but rather because it allows the phenomenon I am illustrating to be clearly seen. The diagram shows a phase change. On the left, the solid particles are loosely packed. There are lots of spaces between them. In those spaces can be found the moisture associated with the cargo (the blue areas). The particles are in contact with each other and the water (blue) is simply present. It doesn’t do anything.
Follow the wavy arrow to the right hand side; there to represent the input of energy in the form of vibration during a sea passage. In the right hand image, you will find exactly the same circles/spheres. Here however the whole assembly occupies a smaller volume than did the left hand image. Thus the input of energy has resulted in consolidation of the cargo into a smaller volume. Further, the image shows blue water throughout the interstitial spaces.
The point the image is illustrating is that the sequence of events involves consolidation/compaction as a consequence of the input of energy. The same volume of solid particles is now associated with less interstitial volume and, if there is enough moisture present, that might result in the water filling the voids on the right hand side when it did not on the left. Liquefaction. The particles on the right are separated by water and it is the water which governs the bulk properties. Pore water pressure is the name given to the pressure associated with the water in the spaces, and in a liquefied stow it is the pore water pressure which supports the cargo above. Water, being a liquid, is nearly incompressible – the volume of water stays the same at all times, it is the volume of the interstitial pores which changes.
The Proctor/Fagerberg test works on this principle – the test is designed to measure the amount of water expressed as a volume percentage of the available space (void/interstitial). Thus the image on the right of my diagram would be 100% saturated in Proctor Fagerberg terms. The energy input in the Proctor test comes from a slide hammer pounding the surface of the sample. I will write about the tests and how they work in a later article.
Many of the provisions in the IMSBC Code (or BC Code as it was a number of years ago) arise from studies carried out on samples of metal concentrates. It is worth remembering this when consulting the Code even today. Concentrates are a semi-manufactured intermediate product and tend to be very consistent in terms of particle sizing. The provisions in the Code allow for TML certification to be up to six months prior to the voyage. These make sense if we are dealing with a cargo of concentrates from a process which churns out parcels of that commodity which are very much the same in terms of flow properties from month to month, even year to year. The same provision makes no sense whatsoever when dealing with shipment of nickel ore or iron ore fines; these receive little processing prior to shipment and the flow properties depend on the geological conditions in the mine.
There are a number of phenomena reported regularly when vessels are affected by liquefaction. As I have said above, the cargoes tend not to behave like liquids, but rather very dense fluids. The stow may flatten out – an untrimmed/peaked stow may turn into a wholly flat surface. There may be water expressed to the surface of the stow. Look at my diagram above – on the right hand image there wasn’t enough room for the inherent moisture and some of it ended up on top of the cargo. That water is simply a liquid and will be free to form a free surface. A free surface of water will affect the stabilty of the vessel but often the amount of water actually on the surface isn’t large, even though it may look spectacular when in motion.
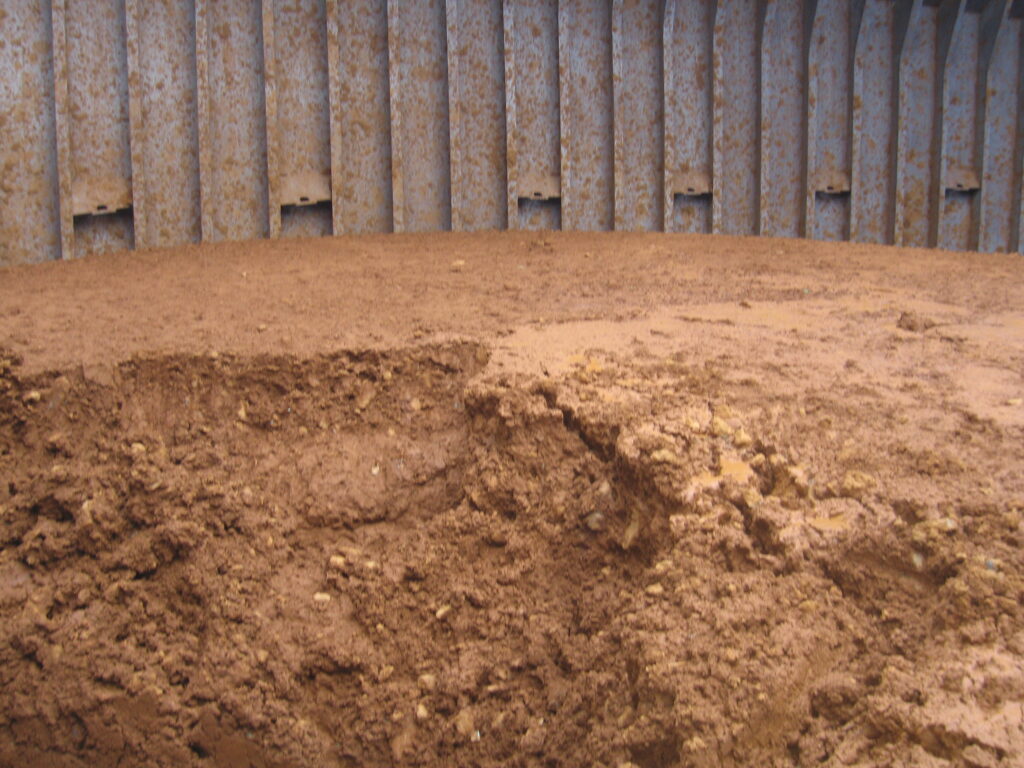
When many cargoes liquefy, the whole stow, or large parts of it, can become mobile. That is a result of the particle to particle contact being prevented by the interstitial water. There are often reports of the vessel taking on a list. This tends not to be an angle of loll, but rather a result of the cargo moving. What can happen is that when the cargo becomes mobile when in a fluid state, it moves to one side with the natural roll of the vessel. It then doesn’t return to centre when the vessel rolls back. Gradually, over a number of roll periods, the cargo takes up position biased towards one side of the hold, resulting in the list. This is of course very dangerous as eventually that list may become large enough for down-flooding with sea water to occur. This is one example of liquefied cargoes not behaving as liquids as it is the asymmetric behaviour of the cargo which results in the list developing.
The case of bauxite as highlighted by the tragic loss of the BULK JUPITER and the lives of 18 of her crew members is interesting. Work followed which resulted in new provisions in the IMSBC Code for Group A bauxite cargoes. It has been strongly argued that bauxite does not undergo liquefaction, and a new term “dynamic separation” has been coined to describe its behaviour. This BIMCO article has a clear description of the difference between dynamic separation and liquefaction. In dynamic separation, the cargo splits into two phases. A lower phase containing the cargo solids is initially immobile despite being saturated with water. It is not in a liquefied state. There is however a volume of free water expressed to the surface (which may be a slurry containing some very fine particles of solid cargo). That water phase is mobile and the risk to the ship’s stability comes from the free surface effect of the water. Only when the vessel’s stability has been compromised by the free surface effect to produce a substantial list might the lower solid phase move.
The new bauxite fines schedule has an interesting provision.
An atypical motion of the ship (wobbling) may also be indicative of cargo instability and the master shall consider appropriate action.
IMSBC Code 2020 Edition
I have heard presentations from members of the bauxite working group where this “wobble” was stressed as one of the clear “red flag” moments a vessel should be watching out for when carrying bauxite fines. A video is often shown which was produced by AMSA to illustrate the behaviour of vessels encountering dynamic separation. I would encourage the reader to watch it carefully.
It is important to note that the video does not show anything liquefying. The motion seen by the model in the video is governed by its buoyancy and the motion of the steel balls in the tracks. Those tracks are shaped to produce a harmonic motion rather like a pendulum. Having two or more balls on the tracks at the same time produces a form of coupled motion. Coupled harmonic oscillators can exhibit extremely unpredictable behaviour. The well-known Rotts Pendulum is an example – this couples two pendulum rods with different lengths and weights. The resulting behaviour can swap back and forth between wobbles and seemingly random modes.
The AMSA video is simply showing coupled harmonic oscillators on a floating system. As an illustration of the consequences of dynamic separation this is appropriate because it is a free fluid phase (the expressed water) which is compromising the stability. This is not the same mechanism which gives rise to the asymmetric behaviour I have described above for cargoes undergoing liquefaction.
For a vessel at a port loading a cargo, the distinction between liquefaction and dynamic separation isn’t obviously significant. Both are behaviours exhibited by Group A cargoes. Both require a TML to be certified and require the moisture content of the cargo to be below the TML for safe carriage. Many natural unprocessed ores contain a mixture of different minerals. Thus the distinction between nickel ore, iron ore and bauxite may depend more on the intended processing and use than the actual make-up of the ore itself.
Vessels carrying Group A cargoes have successfully reached discharge port with mobile cargo in one or more holds. It is however a huge risk. Similarly, carriage of cargo which is overmoist does not necessarily result in either liquefaction or indeed in the vessel getting into difficulties.
The reverse however is clear. To the best of my knowledge, no vessel has loaded cargo which meets the criteria of the IMSBC Code (i.e. with average moisture properly below a reliably tested TML, properly trimmed) and has subsequently had difficulties with cargo liquefaction unless there has been actual water ingress into the holds.
The message then remains the same as it always has. If you wish to carry a Group A cargo safely (and you should), the IMSBC Code should be followed. That means proper sampling being carried out prior to loading, and those samples being reliably tested for moisture and a TML established by a laboratory properly equipped and experienced in carrying out the tests in question. In my opinon there is no substitute for this which can guarantee the same degree of safety.
One thought on “Liquefaction – some basics”
Comments are closed.