Absolutely nothing to do with A.A. Milne – sorry!
Iron ore fines
I outlined in last week’s post the three tests which have been a familiar part of the IMSBC Code for many years. In 2009 there were two vessels lost in India carrying iron ore fines – ASIAN FOREST and BLACK ROSE. In addition, there were numerous problems which arose during the loading of other vessels. At the time there was no schedule in the Code for iron ore fines as a Group A cargo. As a consequence, work was carried out resulting in new schedules and a new test. As I noted, the existing three tests came in for some criticism for not giving consistent results across a range of different types of iron ore fines. As a consequence, a new test was developed, which is now a part of Appendix 3 of the Code.
That test was based on the Proctor/Fagerberg test, and is referred to in the Code as the “Modified Proctor/Fagerberg test procedure for iron ore fines”. This test methodology makes it clear that it should only be used to test samples of iron ore fines.
The standard equipment set was used but with a much lighter compaction hammer. This hammer weighs only 150g – less than half the mass of the standard hammer. The size of hammer required for the test was established by reference to work on the conditions experienced in a typical stow of iron ore fines, but it is very light indeed and imparts only small blows on the moulded sample. Even toffee hammers weigh more!
Incidentally, in Proctor’s original work on testing soils, the hammer weighed 2.5kg. Reducing the hammer size to 350g (standard Proctor/Fagerberg, referred to as the “C” hammer) and then 150g (modified P/F, referred to as the “D” hammer) provides substantially less energy input.
Unlike the standard Proctor Fagerberg test, the modified test for use with iron ore fines defines TML as the moisture required to produce 80% of saturation level. The justification for moving the critical point from 70% to 80% is touched upon in the wording of the test methodology in the Code. It says.
Optimum moisture content (OMC) is the moisture content corresponding to the maximum compaction (maximum dry density) under the specified compaction condition. … This test procedure was developed based on the finding that the degree of saturation corresponding to OMC of iron ore fines was 90 to 95%, while such degree of saturation of mineral concentrates was 70% to 75%.
IMSBC Code 2020 Edition, Appendix 3.
The concept of OMC is an important one. Imagine a sample with no water at all. Compaction using the hammer will result in a density which is governed by the intrinsic density of the solid material in the sample together with how well it packs into the mould (i.e. how much air remains after compaction). When water is added, initially the water will assist in lubricating particle to particle contact and will fill some of the voids – thus the density will increase because there is water in the gaps rather than air. Eventually, further additions of water will result in some free water within the sample mould because the voids are as filled as they can be. Because the density of water (1 kg/m3) is lower than the particle density of the ore being tested, adding further water serves to reduce the overall density. A mathematician would refer to this as a “turning point” in density, and the highest density happens at a moisture content known as OMC. OMC will depend on the compaction conditions – i.e. the weight of the hammer and to a lesser extent the shape and size of the mould.
Hence reasoning behind having a higher criterion for TML in iron ore fines. As the Code says, the iron ore fines samples studied had a higher saturation at OMC than was found when studing mineral concentrates using the Proctor/Fagerberg test. The aim is to set a TML which maintains a good safety margin (recall that for the flow table test and penetration test, TML is generally set at 90% of Flow Moisture Point). The reported fact that iron ore fines can typically attain a higher saturation than do concentrates means that the TML can be safely set to a slightly higher saturation level (80% rather than 70%). Well, that’s the theory.
As noted above, the modified Proctor/Fagerberg test for iron ore fines is only applicable to that cargo. This was the first time a TML test had been written into the IMSBC Code which related only to a specific cargo. Note that there is no prohibition on using any of the the original three tests on iron ore fines. The modified Proctor/Fagerberg test for iron ore fines is likely to give higher TML figures than would using any of the other three standard tests. It is odd that one of the driving forces beind the development of the modified test was that the existing three tests did not give consistent results. We now have a situation where a sample of iron ore fines can be tested by any of four methods, and these do not give similar results to each other.
Coal
The next method found in the Code is a modified Proctor/Fagerberg specifically for coal.
It is curious that the standard Proctor/Fagerberg method in the IMSBC Code contains the following statement
This method should not be used for coal or other porous materials.
IMBC Code 2020 Edition, Appendix 3, methodology for standard Proctor/Fagerberg
The way this provision is written is suggestive that the underlying reason the standard Proctor/Fagerberg method is unsuitable for coal samples is because coal is porous.
The modified method for coals uses a similar overall procedure to the standard Proctor method but the vessel has a larger diameter. The test method calls for a “hammer equivalent to the Proctor/Fagerberg D energy hammer” – more on this curiously worded requirement below. Critical moisture is set at 70% saturation, which is the level used in the standard test. If 70% of saturation cannot be attained in the test, the conclusion is that the cargo is not liable to liquefy. It is not clear to me how this addresses the implied difficulty in testing coal/porous materials implied by the wording of the standard method.
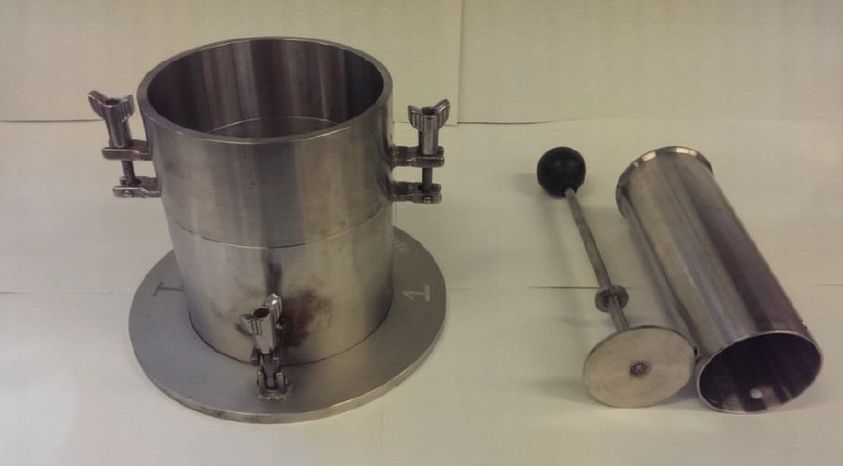
As noted above, the coal test method calls for a hammer equivalent to the D type energy hammer. That is the hammer developed for use with the iron ore fines test, which weighs 150g and has a foot diameter of 50mm. However, the image of the equipment for the coal test shows a different hammer. This has weight 337.5g (nearly as much as the standard C type hammer of 350g). However, the diameter of the foot is 75mm whereas the size of the standard D hammer is 50mm across. Thus the hammer shown for the coal method is heavier than the iron ore fines hammer but has a larger foot. It is equivalent because
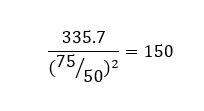
The most striking novel feature of the coal Proctor method is a procedure to create a reconstituted working sample where the coal contains particle sizes in excess of 25mm. Many commonly traded coal cargoes are sized up to 50mm, and so many real world coal cargoes will require the reconstitution procedure to be applied. The reconstitution process involves removing “oversize” (i.e. over 25mm in size) and then adding back calculated proportions of smaller particles from the working sample to replace the removed oversize fraction.
I mentioned in my earlier post on testing that a work-around to deal with oversize was in widespread use for nickel ore. The reconstitution process for coal samples is a part of the new modified Proctor/Fagerberg test for coals and is the first approved means of testing samples with particles larger than 25mm.
Many types of coal are not capable of liquefying and are thus not Group A cargoes. Very helpfully the new test contains criteria for determining if a coal is liable to liquefy.
I note that the new modified method for coal states that it requires a minimum of 170kg for a test to be carried out.
There are now three tests which can in theory be used for coal – the flow table test, the penetration test and the modified Proctor/Fagerberg for coal. The new coal test contains a number of elements which are not present in the flow test or penetration test – i.e. the ability to modify samples to allow for the presence of much larger particles and the existence of a diagnostic check in the test to determine whether a given coal is Group A or not.
Bauxite
The final method is specific to bauxite. The existence of this test came about as a consequence of the BULK JUPITER sinking and the work carried out which established and characterised dynamic separation as relevant to bauxite.
This modified Proctor/Fagerberg test uses the same larger diameter mould called for to test coal. The hammer is the lighter “D” hammer per the iron ore fines method in its 150g diameter 50mm form.
The bauxite method also contains a method for making a reconstituted working sample by removing oversize and substituting smaller material according to a formula/recipe.
The critical saturation level is set at 70% for some bauxites and at 80% for others. The decision between 70 and 80% saturation as the critical point is made by reference to the optimum moisture content – i.e. the highest saturation attained. This choice has at its technical base the same fundamental issue which is given as the rationale for applying a critical level of 80% in the modified test for iron ore fines as discussed above.
As I have discussed in an earlier article, bauxite is said not to undergo liquefaction in the normal sense, but rather to exhibit dynamic separation when overmoist. Dynamic separation is a different failure mechanism to liquefaction. However, the test introduced to ensure safe carriage and a suitable TML is largely the same as that applicable to iron ore fines.
This test is relatively new, and I have personally only seen it in action once. That particular bauxite formed large clay-like lumps with the addition of water and the 150g hammer was not capable of packing the ore into the Proctor mould except at very low moisture contents. Some bauxite types may be more suited to testing using other methods.
Concluding remarks
The recent proliferation of new cargo-specific versions of the Proctor/Fagerberg, together with the three more established standard methods presents a somewhat bewildering picture. Shippers involved in trades for coal, bauxite or iron ore fines will have the option of instructing a laboratory to carry out the cargo-specific test or one of the standard ones. Different commodities may involve the reconstitution procedures to accommodate substantial oversize. For commodities where no “new” cargo-specific test exists, the laboratory will have no established reconstitution procedure and will have to deal with oversize particles in an ad-hoc manner.
Clearly this is unsatisfactory. If reconstitution works for coal or for bauxite, it would be expected that a similar procedure might work for iron ore fines with oversize, or indeed nickel ore which tends to have oversize.
If it is acceptable to relax the Proctor/Fagerberg critical saturation percentage to 80% for iron ore fines and some bauxites, why is it not acceptable to apply 80% to any cargo which has an optimum moisture content (OMC) of over 90%?
If the studies showed that the new tests provide an appropriate TML for bauxite, iron ore fines and coal, where does that leave the “standard” methods in relation to these commodities? My understanding is that the modified Proctor tests introduced recently for these specific cargoes in a number of instances produce higher results for TML (i.e. the cargo can be shipped with higher moisture content). Perhaps the extra safety margin associated with the older tests was unneccesary.
It is possible to attempt to use the new tests for coal and bauxite and be directed by the test protocol to a conclusion that the subject cargo is not Group A. There are criteria in the schedules for iron ore fines, manganese ore fines and bauxite which set out technical parameters for what constitutes a Group A cargo of that mineral. There are no test procedures or criteria available for other materials to determine whether a given substance is Group A or not.
A number of materials mined and subject to relatively little processing contain a variety of minerals. For instance, an ore may contain nickel and also substantial amounts of iron. If an ore from Malaysia contains aluminium and also iron in oxide form, is it bauxite, or is it iron ore?
In my opinion, the proliferaton of multiple cargo-specific tests makes life very much more complicated for those involved and is not a helpful development. I believe it would have been preferable to revise the test methods in the Code to have either a single available test or a number of tests with the selection prescribed by the Code, rather than a “choice”. As always, however, we recommend adhering to the provisions of the Code wherever possible.