Chain Reactions – Fertiliser
One of the most interesting concepts arising out of the science of carriage of goods at sea is the phenomenon of bulk behaviour being different to the lab-scale behaviour of a commodity. Later articles will keep returning to this theme, but today’s topic is chain reactions, and one in particular which can take place on ships with disastrous consequences.
In this article, I will use the term chain reaction to refer to a chemical or physical reaction where some of the products of the reaction are the same as the reactants themselves.
One spectacular example of this is nuclear fission. One particular uranium isotope has the property that, when its nucleus is hit by a neutron, it splits into two smaller fragment nuclei, releasing three neutrons and energy. Each of those three neutrons can, in theory, cause fission of another uranium nucleus, leading to a chain reaction which can rapidly release enormous amounts of energy – a nuclear explosion. Nuclear reactors use chain reactions but have control rods to absorb some of the neutrons to slow the chain reaction down to desirable levels.
Nuclear reactions on cargo ships are, fortunately, unlikely! Chain chemical reactions can occur on ships, and the results are very problematic.
The cargo this article will focus upon is a particular category of fertiliser. Lots of fertilisers are carried by ships in bulk, usually with no ill effects. Fertilisers in general are categorised by the amounts of nitrogen (chemical symbol N), phosphorus (P) and potassium (K) they contain as these three elements supply much of the inorganic mineral requirements for growing plants. The form in which the N, the P and the K are present influences how readily it can be taken up by the plant and used. Compound fertilisers are often called “NPK fertilisers”.
Nitrogen can be present in a number of forms, including as positively charged ammonium ions (NH4+) or negatively charged nitrate ions (NO3–). Ammonium nitrate, NH4NO3 contains both of these types of nitrogen and is a highly desirable source of nitrogen in fertilisers. Unfortunately, ammonium nitrate is not only unstable, but it forms mixtures with combustible materials which are potent explosives. Carriage of ammonium nitrate is therefore highly regulated by the IMO in packaged form and in bulk.
There are a number of schedules in the IMSBC Code for different types of ammonium nitrate. I’m not going to discuss them all in detail here – if you have a query regarding carriage of ammonium nitrate materials or fertilisers generally, please do get in touch. However, some of the less hazardous materials containing ammonium nitrate are classified as “ammonium nitrate based fertiliser”. One of these is a “non hazardous” Group C bulk cargo schedule. Group C cargoes in the IMSBC Code have no designated chemical hazard requiring special precautions.
The criteria for being considered non-hazardous are set out in the IMSBC Code and do not make easy reading. The clause we are concerned with here is this one
uniform ammonium nitrate based fertilizer mixtures of nitrogen, phosphate or potash, containing not more than 70% ammonium nitrate and not more than 0.4% total combustible organic material calculated as carbon or with not more than 45% ammonium nitrate and unrestricted combustible material. Fertilizers within these composition limits are not subject to the provisions of this schedule when shown by a trough test … that they are liable to self-sustaining decomposition or if they contain an excess of nitrate greater than 10% by mass
IMSBC Code 2020 edition
Phew! Put in simple terms, to be non-hazardous, your ammonium nitrate fertiliser must not “fail” the trough test. The trough test is a test designed to detect fertilisers capable of undergoing self-sustaining decomposition (SSD). Self sustaining decomposition is a chain reaction which some compound NPK fertilisers which contain ammonium nitrate can undergo. Here, the chain reaction is the thermal decomposition of the fertiliser. When exposed to heat, the fertiliser granules decompose, releasing toxic nitrogenous gases and some heat.
These decomposition reactions only take place when the substance is heated. The heat evolved by the reaction taking place within a cargo can then travel to adjacent granules and cause them to decompose – and hence a chain reaction. In a fertiliser undergoing self-sustaining decomposition, that reaction can continue even when the source of heat is subsequently removed, and it can spread through a bulk.
Crucially, it is the interplay between
- how much heat is required to initiate the decomposition
- how much heat is released from the reaction
- how much inert (non decomposing) material there is in the cargo
- and how easily heat released can be lost to the surroundings
which governs whether the chain reaction can be sustained or will just die out.
The principle of the trough test is straightforward. The trough itself is a gauze mesh constructed to specific dimensions specified by the test method. The trough is filled with the fertiliser being tested and one end is heated until the heated fertiliser decomposes. The material “fails” the test if decomposition then propagates down the length of the trough.
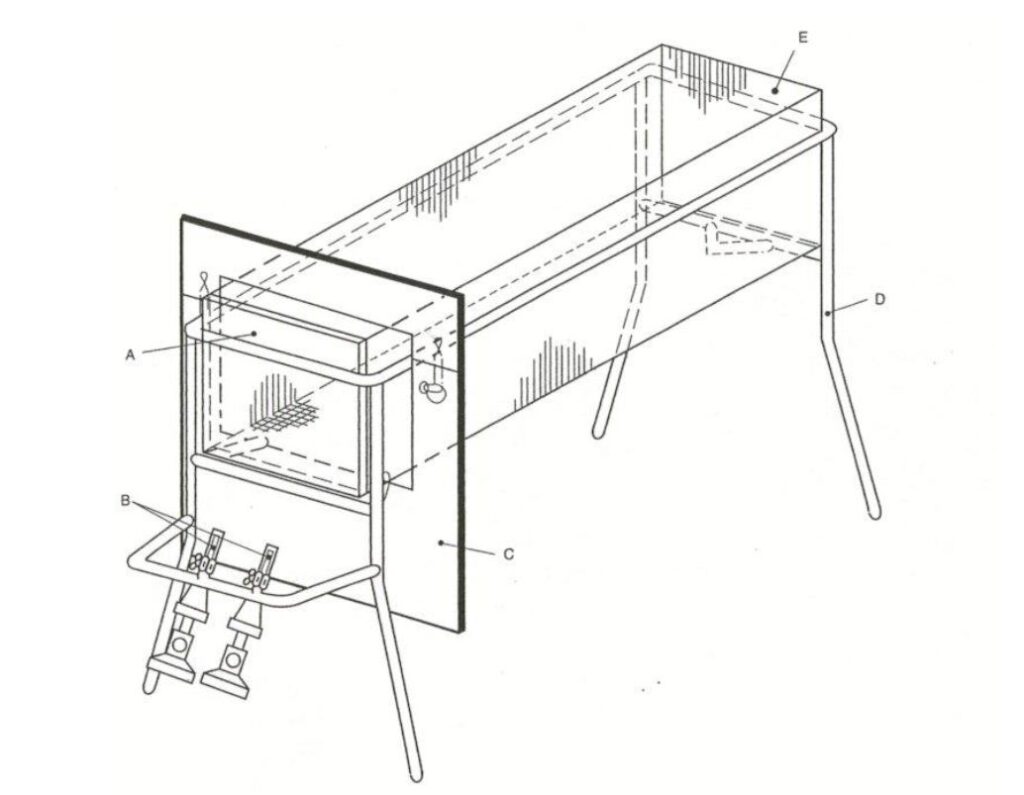
Here is a photo of a trough test taking place. The wires in the photograph are for thermocouples to detect temperature rises, but you can see if decomposition propagates just by looking at the sample in the trough.
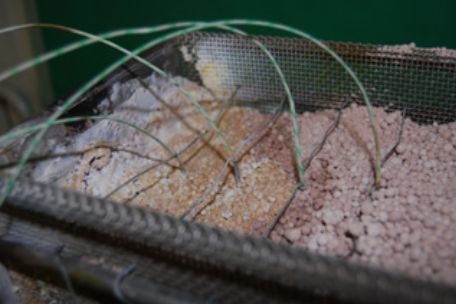
On a ship, self-sustaining decomposition tends to be initiated by a heat source as simple and straightforward as a cargo lamp or bulkhead lamp in a hold. It is an unfortunate fact that many cargo fires on ships are started by lights – that fact itself is an important enough topic to require an article of its own.
By the time the problems are detected, the situation in the hold tends to be very well established. Copious amounts of fumes are emitted, resulting in crews having to abandon ship, and some vessels have even been destroyed. It is very easy to find spectacular images on line of enormous plumes of gases, some of them toxic, emanating from vessels such as CHESHIRE, PURPLE BEACH, OSTEDIJK, and others. These vessels loaded parcels of ammonium nitrate fertiliser, non-hazardous, in each case certified by means of the trough test as non-hazardous. So was the cargo in the trough in the photo above. During the test being carried out in the photo above, despite repeated test runs, no significant propagation of decomposition was ever seen.
In each case then, significant events involving self-sustained decomposition of large amounts of fertiliser took place despite the cargo purportedly not being capable of that reaction.
As a result of the CHESHIRE incident, the Isle of Man Ship Registry published an incident report which contained the following very telling extract
1) A thermal decomposition of the Ammonium Nitrate Based Fertiliser (non-hazardous) cargo commenced and despite arrest attempts being made, continued to its conclusion on board Cheshire.
2) Guidance submitted to the IMO by fertiliser industry bodies emphasises that ammonium based fertilisers can be safely transported, provided existing safeguards are followed. These safeguards are evidenced as having been carried out on Cheshire, yet a thermal decomposition still initiated.
3) The UN S.1 “trough test” is used to determine self-sustaining decomposition properties of ammonium nitrate based fertiliser to classify the Cargo Group. The individual grades of cargo carried on Cheshire passed the S.1 test and were thus classified as “Cargo Group C” (non-hazardous) six months prior to shipment on Cheshire.
IOM Ship Registry Casualty Investigation Report CA 128
The report called for research into whether the trough test is appropriate for fertiliser in bulk. Intercargo reportedly stated that “it is clear from the Cheshire incident that this cargo, or at least some of the ammonium nitrate-based fertilizers shipped as this cargo, should not be treated as group C”.
The problem associated with the trough test seems to be that heat is too readily lost from the material in the trough. The purpose of the test is to provide a lab-scale means of detecting whether self-sustained decomposition can take place in large bulks. It doesn’t reliably do that in all cases.
Late in 2021, litigation regarding the CHESHIRE in the Norwegian Appeal Court was reported by law firm Simonsen Vogt Wiig. They say that the Appeal Court concluded amongst other points that the cargo had been correctly classified in accordance with the IMSBC Code and that the hold lighting system should have been disconnected prior to the voyage. The fertiliser manufacturers thus were reportedly successful against the vessel Owners and Charterers.
We therefore have a situation where a cargo can be categorised as “non-hazardous” because it passes the mandated test (by not exhibiting a certain property in the lab conditions). However, the actual cargo then exhibits that property on the voyage. Simonsen Vogt Wiig say that the loss associated with the Appeal Court judgement was at least USD 30 million.
Carrier beware!
Cocoa – commodities and their carriage
As most people will be aware, chocolate comes from cocoa, a product of the plant Theobroma cacao. Most chocolate we consume is sweetened to Western tastes and may contain significant amounts of milk. Chocolate makes use of fats extracted from cocoa. These fats take on a number of crystalline forms at room temperature and have melting points such that chocolate begins to melt and soften in the mouth. These physical properties contribute to the experience of eating chocolate which make it so pleasant.
Cacao trees are grown and harvested in countries in South America, West Africa and also in Indonesia. Most processing takes place elsewhere, requiring cocoa materials of various types to be shipped to those locations.
Cocoa beans form embedded in a fleshy pulp, in pods on the cocoa tree. The harvested beans are subjected to a process known as fermentation, generally in the country of harvest. The fermentation process is an essential stage in developing the flavours and colours we associate with chocolate. Traditionally, it takes place in wooden boxes covered with banana leaves. It is actually the pulp which undergoes the fermentation (i.e. microbiological activity) but the temperatures produced and the enzymes present give rise to a series of biochemical changes within the beans without which we wouldn’t have chocolate.
Once fermented, the beans are dried to below about 7-8% moisture. If this isn’t done, they would deteriorate rapidly and would go mouldy. Traditionally, the beans were then bagged, using jute fibre bags. This was the form of bagged cocoa familiar for many years, often carried on ‘tweendeckers, but now more commonly placed into shipping containers.
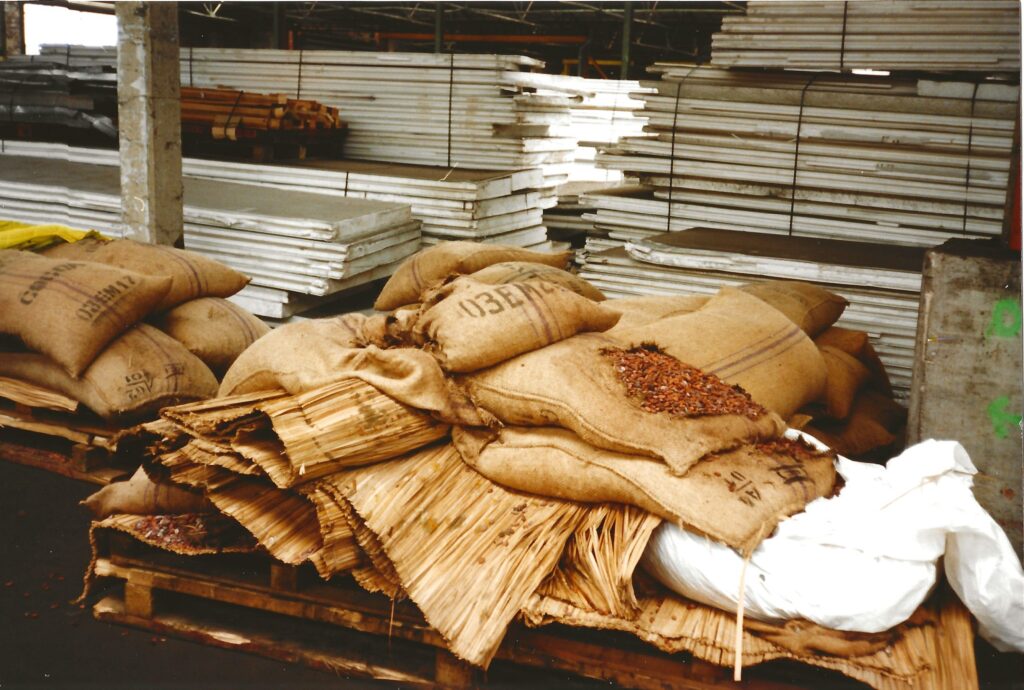
Because cocoa is a high value agricultural commodity, cargo care during carriage is very important. Invariably, bagged or bulk cocoa beans are shipped from a tropical country and are inherently warm when shipped. The beans do not conduct heat to any significant extent and so except at the periphery of a stow, they will retain their heat as shipped throughout a voyage. That is an inevitability, and isn’t a problem except when the ship happens to sail somewhere in a colder climatic region. As large amounts of cocoa processing takes place in Western Europe and North America, there is a likelihood that at least for some parts of the year, shipments of cocoa will indeed be exposed to lower ambient temperatures during a voyage, often substantially so. That’s when the problems can start.
Those problems are associated with condensation – ship’s sweat. That is condensation forming on the steel structures around a cargo when those structures are cooled by external cold temperatures. The condensation can then wet bags of cocoa, leading to the beans going mouldy. With each bag having a value of $100 or more, it is important to prevent condensation as much as is possible. That requires ventilation and correct stowage. Appropriate, efficient ventilation and stowage to avoid contact with steel structures are both crucial to the safe carriage of cocoa beans.
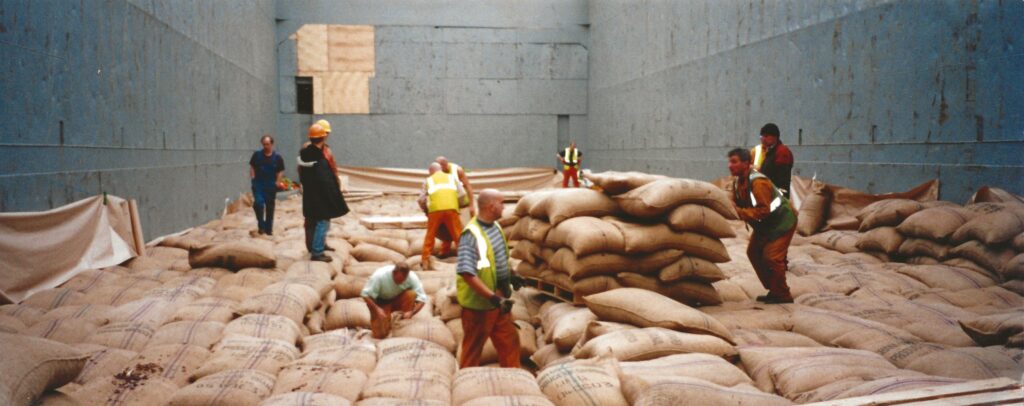
One of the subsequent stages in cocoa processing involves grinding the beans. This releases fats from the cellular structure of the cocoa plant and produces a substance known as cocoa liquor. Although the name might suggest this is alcoholic, it is not. It is a dark brown solid at room temperature, with the appearance and taste of unsweetened plain chocolate. Cocoa liquor is sometimes carried by ships in blocks, wrapped in plastic sheeting and placed into sturdy cardboard boxes.
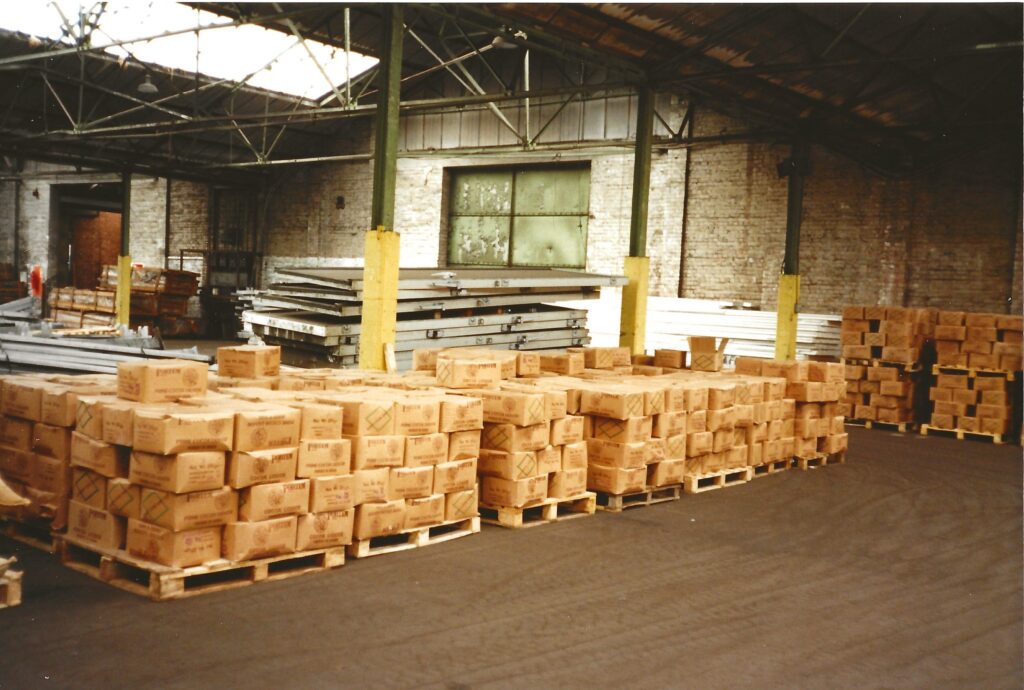
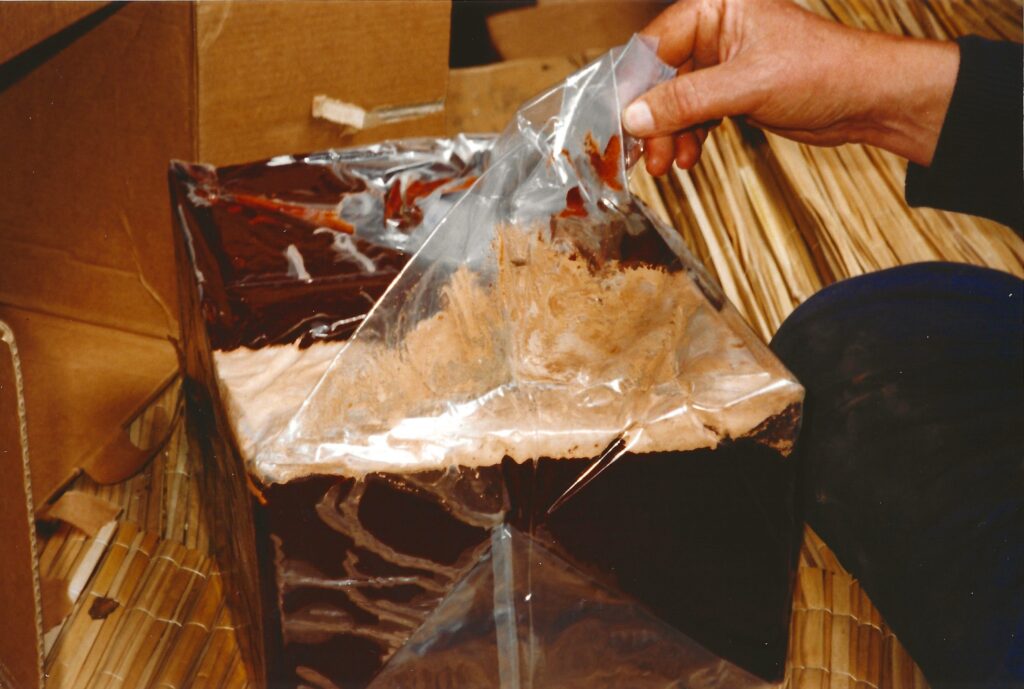
Cocoa liquor can be subjected to a process known as “pressing”. This separates the fats from the cocoa mass/solids. Cocoa fats are known as cocoa butter, pale yellow in colour. Blocks of cocoa butter are packaged similarly to cocoa liquor and carried in shipping containers. The residual cocoa mass after pressing is dark brown in colour and produces the cocoa powder familiar to bakers.
Cocoa fats carried in block form (cocoa liquor or cocoa butter) require careful handling to avoid exposure to heat. Although the blocks are packaged within cardboard boxes, if the contents soften or melt the cartons can collapse leading to handling problems. All cocoa products are sensitive to taint – ships or containers must be clean and free from odours.
Chocolate producers will use blended mixtures of cocoa solids, cocoa butter and cocoa liquor, together perhaps with sugar, milk solids and lecithin to produce different types of chocolate (plain chocolate, milk chocolate, white chocolate). Lecithin is a phospholipid extracted during the degumming of some edible oils such as soya bean oil.
Finally, it is important to know your commodity. It may seem obvious but the properties and behaviour of different commodities produced from cocoa depends on the fundamental physical and chemical parameters of those commodities. Understand these, and apply good cargo care to avoid problems.